Private residential building from 10.09.2022, Kiev region, Vasylkiv.
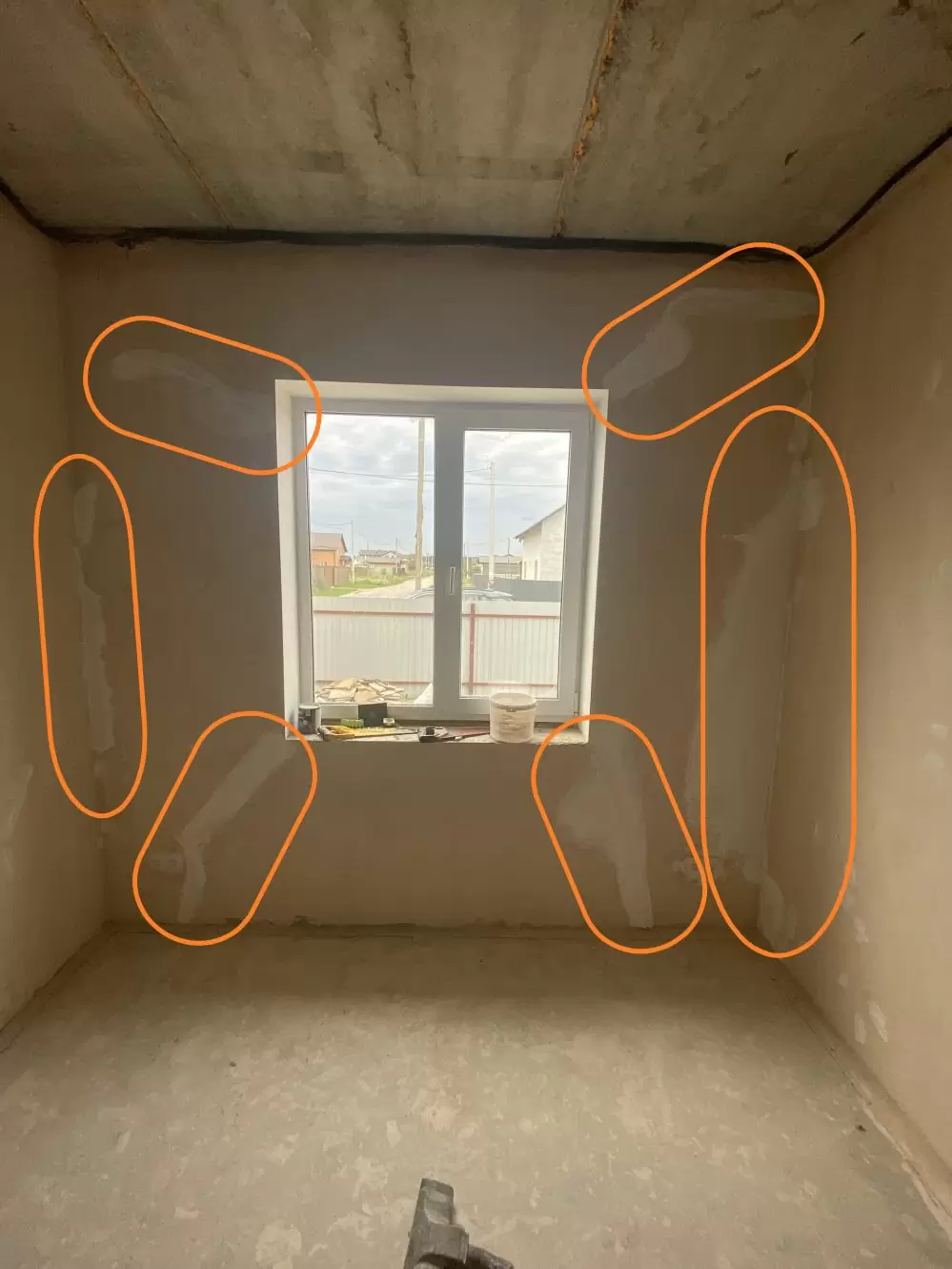
Popular articles
22.05.2024
Introduction
Home renovation in rural areas of Ukraine presents special challenges due to historical, economic and social factors. These houses often bear witness to a long and complex history, ranging from the Soviet period to modern changes. The approach to renovating such buildings requires taking into account both the preservation of their historical value and the provision of modern standards of comfort and safety.
Home renovation in rural areas of Ukraine presents special challenges due to historical, economic and social factors. These houses often bear witness to a long and complex history, ranging from the Soviet period to modern changes. The approach to renovating such buildings requires taking into account both the preservation of their historical value and the provision of modern standards of comfort and safety.
08.05.2024
Property owners often face the problem of cracks in the walls of their homes. One of the methods to combat this problem is to tighten the house, that is, eliminate cracks by bringing its structure into an equilibrium state. In this text we will look at the causes of cracks, methods of tightening a house and the consequences of such actions.
Causes of cracks. Cracks in walls can occur for a variety of reasons, including:
Causes of cracks. Cracks in walls can occur for a variety of reasons, including:
05.12.2023
05.12.2023
Get a free consultation
During the consultation, our experts will assess your problem and offer an approximate solution. You can also order a minimal examination for a more thorough and accurate assessment. Leave your contacts and our experts will contact you.
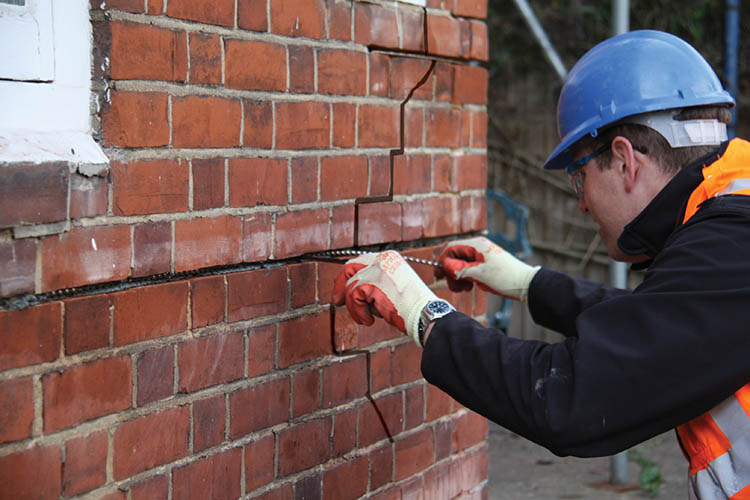